High-Level Indian Auto Industry Delegation Rushes To China To Resolve Rare-Earth Magnet Issue
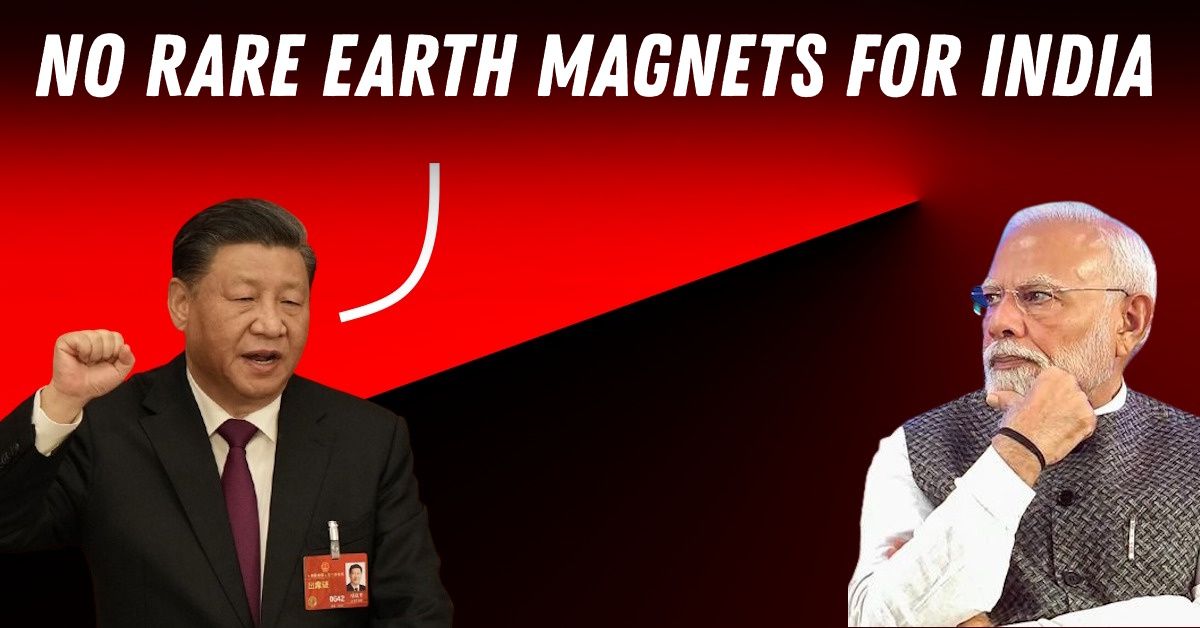
A high-level delegation of auto industry leaders from India has boarded flights to China this week, and the urgency behind the move speaks volumes. The core issue? A worsening shortage of rare earth magnets, a crucial component in electric vehicles and advanced powertrains, which is now disrupting production lines back home. As the world’s largest producer of these magnets, China holds a tight grip over global supply, and India’s growing dependence is starting to pinch at a critical time.
Rare earth magnets are not just small metal pieces. These powerful magnets are used in traction motors that drive electric scooters, electric cars, and hybrid systems. Without them, production lines stall, deadlines slip, and order books go unfulfilled. Most of these magnets, specifically neodymium iron boron (NdFeB), are currently imported from China, and the supply chain has recently become unstable.
This volatility comes amidst stricter export clearance processes in China, higher domestic demand within the country, and logistical delays caused by regional tensions. Several Indian two-wheeler and passenger vehicle companies with aggressive electric portfolios have reported delays in motor assembly and slower product rollout timelines.
While industry insiders have so far managed through small stockpiles and alternate sourcing, cracks are now beginning to show. Some manufacturers have already started slowing down production of certain electric variants. Others are reconsidering the pace of localisation and are putting expansion plans on hold until there is more clarity.
The delegation to China includes senior representatives from key original equipment manufacturers, component suppliers, and auto associations. Their task is twofold. First, they aim to secure immediate shipments of magnets and resolve supply issues with existing vendors. Second, they are expected to initiate talks for more predictable long-term contracts with better visibility on pricing and volumes.
The timing could not be more critical. India’s electric vehicle roadmap is finally showing real momentum, with companies like Tata Motors, Mahindra, Ola Electric and TVS pushing out new models at a fast pace. Production-linked incentive schemes have also created a favourable environment for local electric and battery manufacturing. However, all of this hinges on access to components like rare earth magnets that are still largely imported.
A single hiccup at the sourcing level risks derailing timelines for vehicle launches, weakening competitiveness, and reducing confidence among investors and buyers.
India does have rare earth reserves, particularly in monazite sands found along the eastern coast. However, the country lacks refining and processing capabilities. Extracting usable material is capital intensive, technically complex, and time-consuming. Even with policy support and private investment, it could take several years before India becomes self-sufficient in this space.
In the short term, some companies have experimented with ferrite magnets or motor designs that reduce rare earth use. But these alternatives often come with compromises. They may lower performance, reduce energy efficiency or increase the overall size of the system. These trade-offs are difficult to justify, especially in premium two-wheelers and compact electric cars where performance is a key selling point.
This is why the delegation’s visit is about more than just paperwork or shipping delays. It is a critical effort to secure breathing room while local industries work on building long-term capability.
This shortage may become a turning point for India’s auto component ecosystem. It has exposed how even a single chokepoint in the supply chain can impact broader ambitions.
Some companies are already exploring new sourcing options. Others are looking at joint ventures with Japanese and Korean magnet suppliers. A few are actively engaging with policymakers to accelerate approvals for mining and processing projects.
There is growing discussion around treating rare earth materials as strategic resources. Industry bodies are suggesting that stockpile tracking, early warning systems and diplomatic interventions be included in the future planning of auto and electronics supply chains.
Navigating the road ahead will require a combination of diplomatic skill, industrial resilience and forward-looking policy. On one side is a fast-growing electric mobility market. On the other is a supply chain dependent on a single country.
If the delegation succeeds in securing urgent supplies and smoothing future access, the industry could avoid a prolonged disruption. If not, ripple effects could stretch into the next year. That could delay upcoming launches, increase costs, and challenge India’s goal of becoming a serious global player in electric mobility.